Inventory Counts: The Difference Between Count Tags and Count Sheets.
- Roger Pujol, CPIM, CSCP
- Nov 21, 2024
- 3 min read
Updated: Apr 22
There are two primary methods for recording and reconciling physical inventory counts. These approaches generally apply to traditional and modern ERP Business Software systems, although they might not apply to Warehouse Management Systems (WMS) that use handheld devices. The methods being referred to are inventory tags and inventory count sheets.
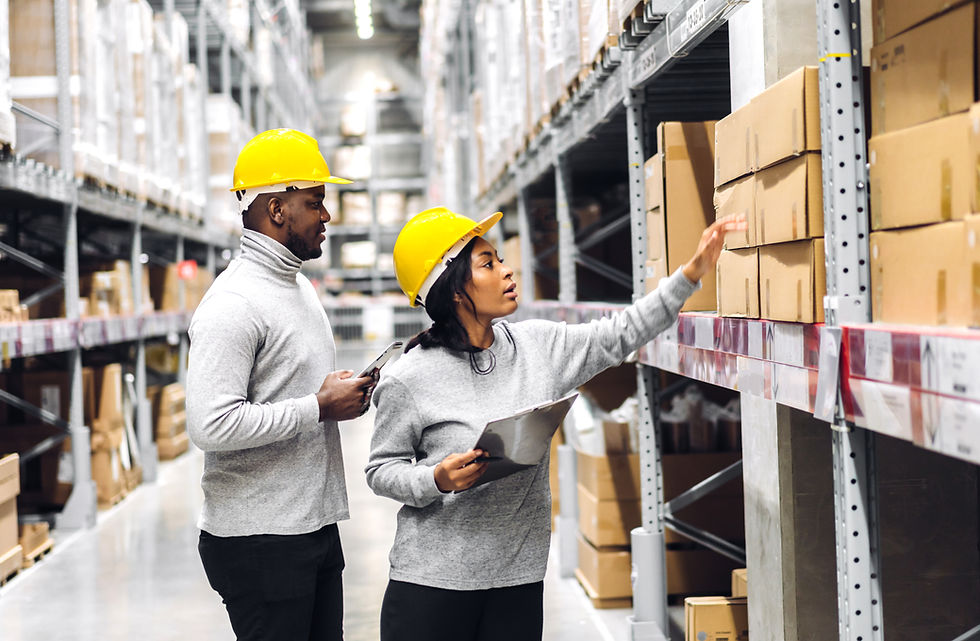
Inventory Count Tags vs. Count Sheets: What is the difference?
Tags begin with the inventory on the floor and then verify it against the computer records. Essentially, tags mean, "This is what we have; match it with the computer data." Count sheets start with the inventory records in the system and then find the items in the warehouse. "This is what the computer indicates; count it against our actual stock." Both approaches strive to achieve an accurate physical inventory count and adjust as needed.

Tag Method
Inventory Tags (Handwritten)
Inventory tags typically consist of a one or two-part document with a sequentially numbered stub, available from major office supply retailers. These tags usually come with numbers ranging from 0001 to 4999. If you need numbers beyond 4999, reconsider your counting strategy. It's advisable to plan ahead to ensure you can secure the necessary quantity of tags within the required ranges before the count date. Additionally, inventory tags need to be manually filled out either beforehand or on the day of the count, which is time-consuming and prone to errors.
Inventory tags are affixed to items requiring counting. During the inventory count day, counters move through sections with count tags, recording the items and their quantities. They tally the items in a designated area and tag each one. The smaller top part of the tag remains with the counted item, while the larger detachable section is handed to the individual responsible for recording and reconciling the count in the inventory management system. The tag number helps ensure easy reconciliation if a counter finds the same item in a different location.

Inventory Tags (Computer Generated)
Most ERP Business Software systems allow users to create custom tags for inventory counts. If you are using the tag method, this is the best approach. By printing the tags in advance, you eliminate all handwriting except for count information such as counter, quantity, and any other necessary count date information. The tag number, SKU number, description, location, and Unit of Measure (UOM) are all pre-printed on the tag.
Computer-generated tags come in two formats: Dot Matrix and Laser. Although finding a dot matrix printer might be problematic these days, they are still available and can be used or reconditioned. Laser two-part forms can be costly, but consider the expense, wasted time, and errors associated with the manually hand-written tags above.

When to use tags?
A limited number of items to count.
The area is small.
Locations are not defined.
The locations are not accurate.
Software is limited.
Inventory is buried.
Inventory might be moved.
Counters are very familiar with the items being counted.
Count Sheet Method
Count sheets are frequently the preferred method. The computer system produces these sheets, which we use to tally the inventory and match it against system records. Counters take the sheets, tally the items, document the counts, and then return the sheets with the recorded data. Count sheets are typically organized by bin location, aisle, rack, or another logical sequence.

When To Use Count Sheets
A large number of items to count.
When the software is capable.
Locations are well-defined.
The locations are reasonably accurate.
Inventory is accessible.
Desire to show on-hand quantities.
Blind Counts?
When utilizing system-generated count sheets, a common question is whether to display the current quantities on hand to the counters. Refer to our post Inventory Counts: Blind Count or Show Inventory on Hand.
Summary
In our workshops on Physical Inventory and Cycle Counting, we focus on teaching optimal methods for organizing and managing warehouses. Our goal is to attain the highest level of inventory accuracy and enhance the overall counting efficiency. Preparation, organization, and training are essential to reaching this goal.
If you need any help with your counting strategy, don't hesitate to contact us.
Roger Pujol is a business improvement consultant and the founder of Champion Business Solutions, LLC. He speaks and writes about encounters helping small to medium-sized businesses (SMBs) improve their business operations.
© 2024 Champion Business Solutions, LLC
Originally published 11/21/2022.